Pumpenfundamentsysteme: Ein wachsender Trend
Ein wachsender Trend bei der Installation, Reparatur und dem Austausch neuer Pumpen ist die Verwendung eines einteiligen Fundamentsystems. Solche Systeme integrieren die übliche Geräteaufstellfläche (Grundplatte) zusammen mit der Betonsäule (Sockel oder Haushaltsunterlage) zu einer homogenen Einheit. Diese Systeme sparen viel Zeit und Kosten, da sie in einem einzigen Paket vor Ort ankommen, und bieten eine vollständig korrosionsbeständige Struktur, die die Installation beschleunigt, indem viele Schritte im Prozess eliminiert werden. Typische Installationen dauern von Anfang bis Ende weniger als zwei Tage. Das Endergebnis ist eine Lösung mit niedrigeren Betriebskosten, die eine zuverlässige Umgebung für Pumpen und rotierende Geräte bietet.
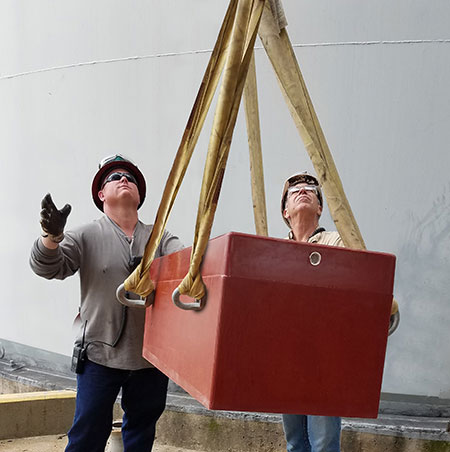
Installation
Bei den meisten Installationen wird ein Betonsockel geformt und fertig gebaut, um eine separate Gerätegrundplatte aufzunehmen. Diese Sockel oder Haushaltsunterlagen dienen zum Anheben von Geräten und helfen, die Mittellinien der Rohrleitungen beizubehalten. Komplette Polymerverbund-Fundamentsysteme werden in einem Stück einbaufertig geliefert und machen Betongerüste und lange Aushärtungszyklen, die mehrere Wochen dauern können, überflüssig.
Kürzlich ersetzte eine große Ethanolanlage in weniger als einem Tag eine Metallgrundplatte mit mangelhafter Mörtelbindung durch ein neues Fundamentsystem. Durch die Verwendung eines schnell aushärtenden Mörtels konnte das Werk in weniger als 10 Stunden den alten Sockel und die teilweise Betonplatte entfernen, ein neues Fundamentsystem installieren und eine Pumpe und einen 150-PS-Motor montieren Anfang bis Ende.
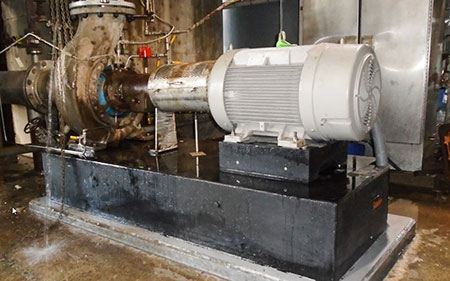
Zusatzfunktionen
Korrosionsbeständige Umgebung
Integrierte Basis- und Sockelfundamentsysteme bieten eine korrosionsbeständige Umgebung. Das Ersetzen von korrosionsanfälligem Metall und Beton macht die Installation und Wartung teurer Beschichtungen überflüssig und schützt die kritische Verbindung zwischen der Gerätebasis und der erhöhten Montagefläche. Darüber hinaus beseitigt der Wegfall freiliegender Ankerbolzen potenzielle Quellen für Kontamination und Korrosion und verleiht der Struktur mehr Leben.
Flache Präzisions-Montageflächen in der Regel innerhalb von 0,002 Zoll pro Fuß Geschwindigkeit der endgültigen Geräteausrichtung, während die hohe Druckfestigkeit von Polymerverbundwerkstoffen vier- bis fünfmal höher sein kann als die von typischem Beton. Konstruktionen, die strukturelle Verstärkungen zusammen mit soliden Konstruktionsoptionen beinhalten, verhindern Rissbildung und machen das Füllen vor Ort überflüssig. Wenn diese einteiligen Systeme in einer kontrollierten Umgebung gebaut werden, kann dies dazu führen, dass eine ordnungsgemäß gebaute und ausgehärtete Struktur bereitgestellt wird. Polymerverbundwerkstoffe bieten Schwingungsdämpfung, während das empfohlene drei- bis fünffache Gewichtsverhältnis von Ausrüstung zu Fundament beibehalten wird.
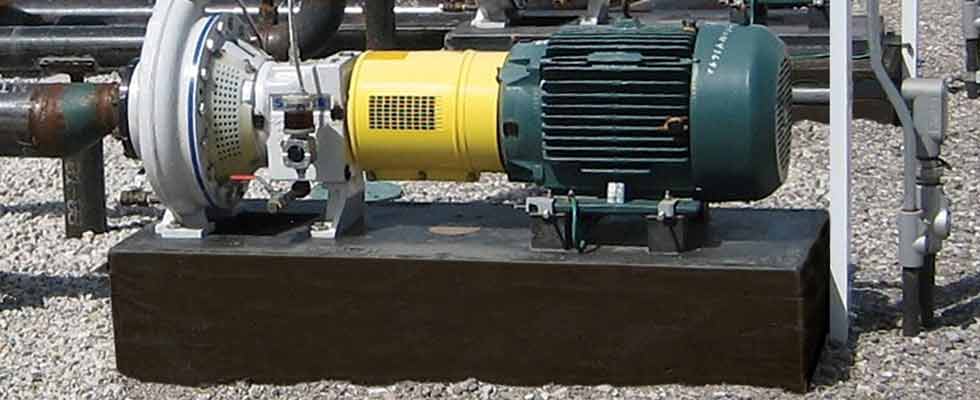
Langlebige und flexible Montageorte
Gewindeeinsätze und Metallmontageplatten aus mehreren Materialoptionen können während des Gießprozesses eingebettet werden, um sichere und stabile Montageorte für Geräte bereitzustellen. Robuste, verstärkte Montageorte übersteigen im Allgemeinen die Festigkeitswerte der Hardware, die zum Sichern von Geräten verwendet wird. Das Hinzufügen oder Reparieren von Gewindeeinsatzstellen zum Anbringen zusätzlicher Ausrüstung oder Ausrüstungsänderungen kann bei den meisten Anwendungen manuell vor Ort vorgenommen werden.
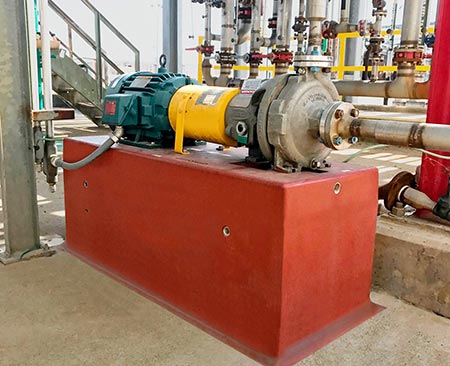
Installationsanordnungen
Fundamentsysteme können in mehreren Anordnungen installiert werden. Sie werden oft mit Mörtel auf der Oberfläche montiert, in einer unterirdischen Umgebung vergraben oder freistehend aufgestellt. Flexible Designs können basierend auf den spezifischen Anforderungen der Ausrüstung, der vorhandenen Umgebung und der Betriebsparameter an viele verschiedene Anwendungen angepasst werden.
Oberflächenmontage
Am häufigsten werden diese Systeme auf einer vorhandenen sicheren Oberfläche verankert und vergossen (Bild 2). Typischerweise wird das vorgefertigte Fundament an der Baustelle ankommen, die auf oder nahe der Entwurfshöhe konfiguriert ist. Sobald das System nivelliert und mechanisch an Ort und Stelle gehalten ist, wird eine kleine Menge Epoxid-Fugenmaterial verwendet, um die Unterseite des Fundamentgusses mit der vorhandenen Oberfläche zu verbinden und abzudichten. Nach dem Aushärten können die Mörtelformen in Verbindung mit der Montage- und Ausrichtungsausrüstung leicht entfernt werden. Diese Aktivitäten finden normalerweise in etwa ein bis zwei Tagen statt.
Einige Konstruktionen können teilweise unter der Erde vergraben und von Kies, Erde oder Standardzement umgeben werden (Bild 3). Eine typische Installation besteht aus einem Hohlraum, der in fest verdichtetem Boden ausgehoben wird, und dem anschließenden Nivellieren des Fundamentsystems gegen eine kleine feste Einrichtung, wie z. B. einen Block. Füllmaterial oder Schnellbeton reichen aus, um die Einheit festzuhalten. Richtig bewehrte Fundamente können sich nicht verbiegen, verdrehen oder blenden, also die Montagefläche
bleibt flach und hält die rotierende Ausrüstung in Ausrichtung. Eine solide Konstruktion kann für die meisten Anwendungen eine angemessene Grundlage für das Gewichtsverhältnis der Ausrüstung bieten. Die Unterflurmontage bietet sowohl eine schnelle als auch sichere Fundamentlösung für Geräte, die sowohl im Innen- als auch im Außenbereich montiert werden.
Freistehende Umgebungen
Fundamentsysteme können auch in einer freistehenden Umgebung für vorübergehenden Einsatz oder auf einer undurchlässigen Oberfläche wie einem mit Gummi ausgekleideten Deich oder einem speziellen Eindämmungsbereich verwendet werden (Bild 4). Strukturen können auf jeder relativ festen, flachen Oberfläche aufgestellt werden und sich mit den Kräften und Bewegungen der Rohrleitungen leicht bewegen. Die Gesamtmasse der Struktur bietet in den meisten Anwendungen eine angemessene Vibrationsdämpfung und eine starre Montagefläche, um die Ausrüstung richtig ausgerichtet zu halten. Epoxidmaterial oder ein Verankerungsgel können verhindern, dass sich Flüssigkeit unter dem Fundament ansammelt. In den meisten Fällen verursacht Bodenflüssigkeit aufgrund der vollständig korrosionsbeständigen Konstruktion der Struktur kein Problem.
Kostenvorteile
Neben den Kostenvorteilen verkürzter Installationszeiten können die Anschaffungskosten geringer ausfallen. Die Arbeit zum Bauen und Setzen von Schalungen, zum Gießen von Beton, zum Entfernen und Abdichten/Fertigstellen von Oberflächen kann teuer sein, um den erhöhten Sockel fertigzustellen. An diesen Sockeln muss außerdem eine Grundplatte für Geräte angebracht werden, um die Installation abzuschließen und für die Ausrüstung bereit zu sein.
In vielen Fällen werden verstärkte Metallbasen mit teuer bearbeiteten Oberflächen spezifiziert, um Steifigkeit und Ebenheit zu erreichen. Diese Metallbasen sind typischerweise Upgrades von Standarddesigns und können die Anschaffungskosten erhöhen. Diese Sockel müssen einer Oberflächenvorbereitung unterzogen und dann auf dem Betonsockel montiert, nivelliert und vergossen werden. Oft ist eine beträchtliche Menge Epoxidmörtel erforderlich, um die hohlen Grundplattenabschnitte zu füllen.
Eine Polymerverbundbasis, die integral in das Fundamentsystem gegossen wird, kann viele dieser Schritte und Kosten überflüssig machen und gleichzeitig die gleichen zuverlässigen Vorteile in einem korrosionsbeständigen Design bieten.
Einteilige integrale Fundamentsysteme bieten eine zuverlässige Lösung und können niedrige Betriebskosten bieten. Sie werden üblicherweise für eine bestimmte Anwendung gebaut und können in vielen verschiedenen Montageanordnungen, Formen und Größen installiert werden. Die Polymerverbundkonstruktion bietet eine lange Lebensdauer in korrosiven Umgebungen und macht zusätzliche Beschichtungen und regelmäßige Wartung überflüssig. Vibrationsdämpfungseigenschaften können eine lange Lebensdauer für rotierende Geräte bieten, was zu einer erhöhten Zuverlässigkeit führt.